The significance of Technical Cleanliness has largely increased in the past years. The widely adopted industry-specific cleaning standards and newly introduced emission norms make cleaning a quality-relevant manufacturing process.
On the other hand, how we interpret the parts cleaning is completely different. We either perceive it as a simple washing step or a costly affair. The story is the same across many industry sectors such as Automotive, Component supply, Aerospace, Precision Engineering, Medical Technology and others.
This article covers the basics of parts washing system, cleaning tasks, cleanliness requirements and why they are important to component manufacturers.
Why Cleaning?
The cleaning of machined components and assemblies is essential for preventing quality issues in modern production processes. The first step in the parts cleaning process is to identify the contaminants, deposits on the surface of the parts and define cleanliness specifications. This ensures the optimal component surface for the further manufacturing process and delivers desired performance and life.
In industrial parts cleaning, the following cleaning tasks can generally be defined:
- Cleaning of undesired material (oil, emulsion particles)
- Removal of passive layers (removal of rust protection oil
- Activation of surfaces
- Protection against corrosion (applying the rust protection oil)
Cleanliness Requirements:
Particularly, in the Automobile industry, contamination can deteriorate the performance of engine and transmission assembly and in turn impact overall lifespan. But the fact is, parts cleanliness is often overlooked by manufacturers. Also, the current production processes are incapable to achieve precise cleanliness results and the industry constantly exploring ways to improve the quality.
To deliver the desired performance and life, the supplier needs to adhere to cleanliness specifications and requirements defined by the OEMs. Keeping this in mind, OEMs usually specifies the permissible limit of particle count in microns, the part should be oil, dust-free, specific Millipore value etc. Some of the examples of requirements are,
- Defined limits for the number of particles. Eg: Particles: < 100 µm
- Achieve Gravimetry < 1 mg
- Continuously higher level concerning the cleaning of parts is required
- Removal of grease, dust, soil
- The part should be absolutely oil-free
- The surface of the part should be completely dry
The specifications could differ depending on the application and the industry.
Cleanliness Standards:
The cleanliness standards describe requirements and methods for determining particle quantity and forms the basis of assessment of technical cleanliness. When it comes to parts cleanliness analysis, ISO 16232 and VDA 19 are integral part of quality management process in the Automotive Industry.
- VDA – 19: German Manufacturers: Particle Contamination of functional relevant Automobile Components
- ISO 16232: International Standards: Cleanliness of components and systems
- Own standards: Custom-defined cleanliness standards by major Auto OEMs
Why there are stringent cleanliness requirements?
As of now, we covered why we need cleaning, what are the cleaning requirements and standards. Now we will see, why the cleanliness requirements are stringent and what are the consequences to the non-conformance of these specifications?
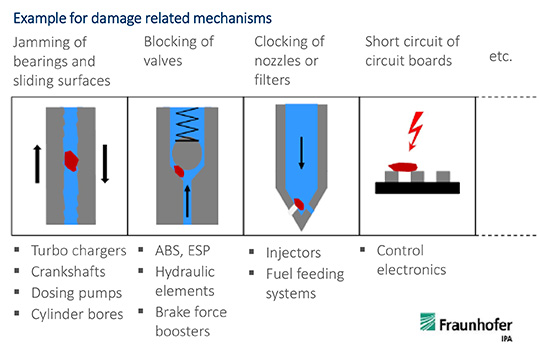
The above picture explains the impact of contamination present on the surface of the part. The presence of particles beyond the permissible limit will affect the functioning of the application. Some of the examples are,
- Jamming of sliding surfaces. Eg: Turbochargers, Crankshafts, Cylinder bores
- Blocking of the valve Eg: Hydraulic systems, Brake systems
- Blocking of the nozzle or filters. Eg: Fuel injection systems
- Short circuit Eg: Circuit boards used in E-vehicles
Thus, the cleaning process should become an integral part of the modern production ecosystem. The selection of materials, fine-tune production processes, deburring process, selection of efficient parts washing machine and, the manufacturing environment plays an important role in achieving critical cleaning quality requirements.
The key to stay competitive is having a mind shift over current production processes and treating Industrial Parts Cleaning as a value-added step rather than simply focusing on the cost.
Watch this space for more information on efficient cleaning process and the influencing factors on cleaning results in our next articles.
For more information on our industrial cleaning technology and machines, contact info.india@ecoclean-group.net or visit www.ecoclean-india.com