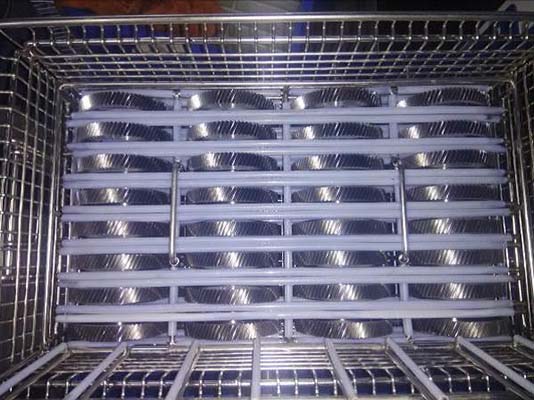
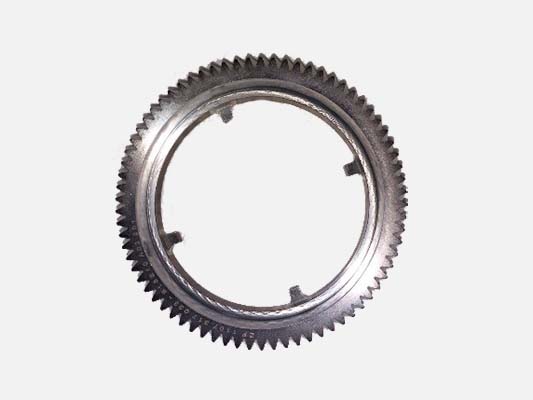
Gear manufacturing process: completing with a cleaning step
Gears, being one of the most important components, demand precise specifications to suit the power transmission applications. Typically, heat treatment, precision cutting, grinding, polishing, buffing and packaging etc. are all integral part of a gear manufacturing process. After these machining processes, it generates the contamination such as oil, fine particles on the surface of the gear.
Removing this type of contamination and achieving required cleaning quality becomes crucial for proper functioning of assembly. Also, it becomes necessary to comply with the basic requirement of technical cleanliness such as ISO 16232 or VDA 19.
This article covers a case study on the requirement of, “cleaning of gears after machining process”, for one of the leading tier-1 manufacturer from India. Using the solution of Ultrasonic cleaning technology offered by Ecoclean, this customer was able to achieve required cleanliness quality.
Cleanliness Requirement:
Contamination | Oil, fine particles, dust |
Process before cleaning | Machining |
Process after cleaning | Packing for end customer |
Cleanliness Requirement | No particle bigger than 600 µm with US as extraction method |
Primarily the customer’s requirement was to remove the oil and dust particles after the machining process and meet a cleanliness of eliminating all the particles bigger than 600 microns with Ultrasonic extraction.
A Solution integrated with Ultrasonic cleaning technology
Cleaning is important as machining operations and critical to process of production. It is also important that cleaning systems are equally effective and efficient. Applications like Gears are usually cleaned in water-based media. The aqueous media is suitable to remove the emulsion, less oil, particles of dirt from machined parts.
To fulfil above requirement, Ecoclean offered an aqueous based cleaning machine “EcoCmini” with three stage cleaning followed by hot air and vacuum drying cycles. Typically, core cleaning process of Injection Flood Wash (IFW) at high flow rate alone is sufficient for these applications. However, as parts were to be tested for gravimetry and particles sizes with Ultrasonic extraction method, the combination of Ultrasonic and IFW cleaning was mandatory.
Right combination of US frequency (kHz) & capacity (watts/liter)
As extraction was to be performed at 40 kHz US frequency, selecting the correct and more aggressive US frequency for cleaning was important. After satisfactory trials at Ecoclean Technology Centre in Pune, optimum frequency of 25 kHz found to be adequate for the desired application.
The selected frequency was also in line with the physics and application of US frequency covered in another Ecoclean blog. Based on test parameters, the gear cleaning comes into the 1st category of frequency ranging from 25 KHz to 40 KHz for large particles with “micro-jet” cavitation.
Moreover, selecting adequate US capacity in terms of watts/liter was another key point for this project. Since, customer specification recommended parts to be tested at minimum of 7 watts/liter of US capacity, Ecoclean decided to install tubular US transducers of 1 kW capacity in 100 liters of cleaning chamber resulting in 10 watts/liter of total effectiveness.
EcoCmini – The compact solution made in India
EcoCmini proved to be one of the best solutions to remove oil and emulsion from mass-produced parts. To fulfill the cleanliness requirement of this customer, it is the best and economical solution. This machine is compact and configured with the processes such as, High power injection flood washing, Spraying, Ultrasonic Cleaning and Hot Air Drying.
EcoCmini has several advantages which includes,
- Best Millipore results
- Modular design
- Low running cost
- Maintenance friendly
- Local service support
To know features, technical specifications and to download brochure of ‘Made in India, EcoCmini’, visit https://ecoclean-india.com/products/ecocmini/